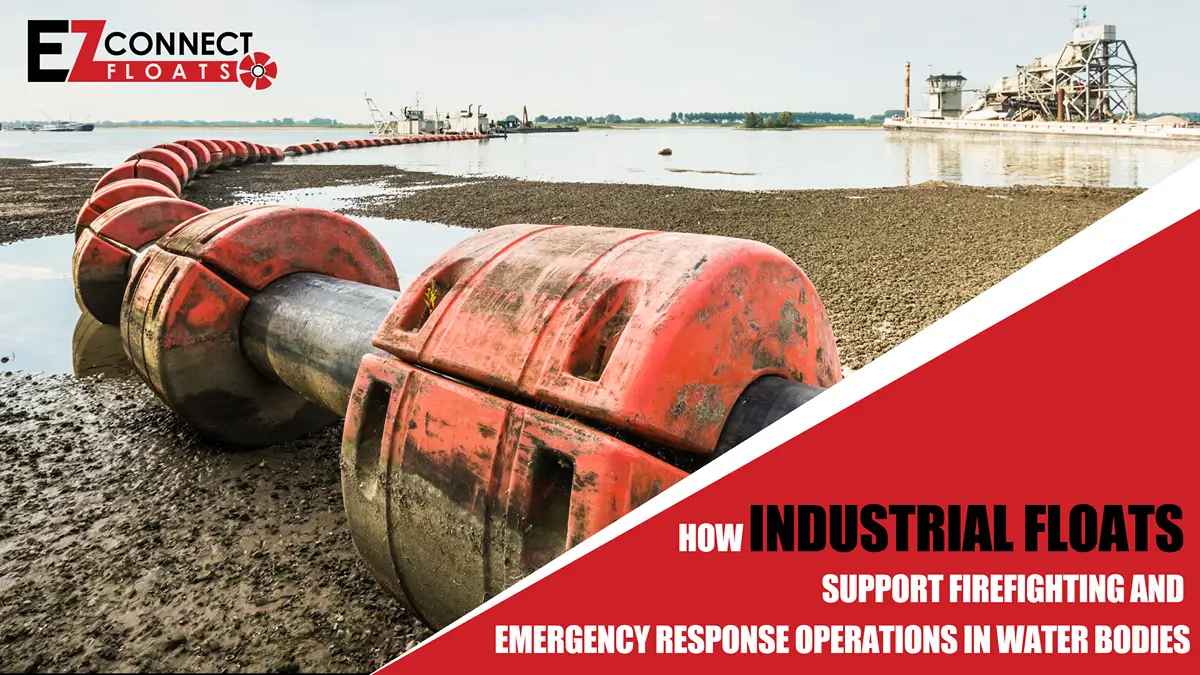
How Industrial Floats Enhance Emergency Response on Water
- Introduction
- Understanding Industrial Floats
- Key Applications of Industrial Floats in Emergency Operations
- Role of Industrial Floats in Firefighting Scenarios
- Supporting Search and Rescue Operations
- Advantages of Using Industrial Floats
- Considerations When Choosing the Right Industrial Float
- Innovations and Trends in Industrial Float Technology
- Conclusion
- Introduction
- Understanding Industrial Floats
- Key Applications of Industrial Floats in Emergency Operations
- Role of Industrial Floats in Firefighting Scenarios
- Supporting Search and Rescue Operations
- Advantages of Using Industrial Floats
- Considerations When Choosing the Right Industrial Float
- Innovations and Trends in Industrial Float Technology
- Conclusion
Introduction
Emergencies that occur on or near water bodies present complex and often hazardous conditions for firefighting and rescue teams. From raging wildfires along coastal areas to devastating floods in urban and rural regions, these operations demand specialized tools and strategies tailored to aquatic environments. Unlike land-based interventions, water emergencies come with added challenges.
One of the most reliable solutions for navigating these complexities is the use of industrial floats. These rugged, high-capacity buoyant devices are designed to support and stabilize a wide array of emergency equipment, ranging from portable water pumps and hoses to modular rescue platforms and pipelines. With the increasing frequency of natural disasters and climate-related emergencies, the need for dependable floatation systems has never been more critical.
At the heart of many aquatic emergency systems are industrial floats, constructed from robust materials like high-density polyethylene (HDPE) or UV-stabilized polymers. Here, industrial floats come into play—keeping the pumps afloat, stable, and optimally positioned for maximum efficiency. Their buoyant support not only maintains operational continuity but also reduces manual labor and deployment time.
Additionally, industrial water floats are instrumental in flood response operations. When cities or towns are submerged, drainage pumps are needed immediately to clear roads, homes, and public infrastructure. These pumps, often deployed in low-lying or submerged areas, are mounted on industrial floats to maintain functionality and prevent electrical hazards. By staying above water, these pumps operate at full capacity without risking internal damage or failure.
Similarly, pipe floats play a vital role in transporting water through hoses or pipelines stretched across water bodies. They prevent sagging, kinking, or submersion of hoses, ensuring uninterrupted water delivery in critical firefighting or evacuation scenarios.
This blog explores how industrial floats, including pipe floats and industrial water floats, support mission-critical operations in aquatic environments. From firefighting and rescue to flood control and temporary utility deployment, these simple yet powerful tools ensure that emergency teams can perform at their best, even under the most challenging conditions. Whether stabilizing high-capacity pumps or providing a safe platform for responders, industrial floats have become indispensable in modern emergency response infrastructure.
Understanding Industrial Floats
Industrial floats are specialized buoyant devices designed to support heavy-duty operations in harsh conditions. Constructed from durable, high-density polyethylene or similar materials, they are engineered to withstand extreme weather, high-impact forces, and prolonged submersion.
Unlike recreational floats, industrial floats are purpose-built to support heavy equipment like pumps, hoses, pipelines, and rescue gear. Their construction allows for flexibility, customization, and easy integration into existing emergency systems.
The most common types include:
Pump Floats
Pump floats are specifically engineered to suspend water pumps above the surface of water bodies such as lakes, rivers, reservoirs, or flooded areas. These industrial floats play a critical role in maintaining the optimal positioning of the pump intake, ensuring it stays clear of sediment, debris, and contaminants that could clog or damage the equipment. By doing so, pump floats not only enhance performance but also extend the operational life of the pumps, especially during prolonged or repeated emergency response operations. Their use ensures continuous water flow during firefighting or drainage activities, especially in remote or inaccessible locations.
Pipe Floats
Pipe floats are essential flotation devices designed to support hoses and pipelines laid across or within water bodies. They securely clamp around the pipes, keeping them afloat and aligned to prevent submersion, tangling, or damage. In firefighting and emergency water transport systems, pipe floats maintain steady water delivery by ensuring hoses remain above water, minimizing the risk of interruptions. Often used in combination with industrial water floats, they are especially critical during flood relief efforts and mobile pump deployments, where long-distance water transfer is needed across challenging terrains.
Modular Platforms
Modular platforms consist of interlocking industrial floats that can be configured into customizable floating structures. These platforms serve multiple purposes during emergency operations: as mobile workstations, staging areas for rescue personnel, or stable surfaces for mounting heavy equipment like pumps and generators. Constructed from durable, weather-resistant materials, modular platforms provide reliable buoyancy and stability. Their flexibility allows responders to quickly adapt the structure to suit mission requirements, whether for firefighting support, flood rescue coordination, or temporary command centers deployed on water.
Key Applications of Industrial Floats in Emergency Operations
Floating Pumps and Suction Systems
During wildfires or flood emergencies, water sources such as lakes or rivers are often utilized to suppress fires or relieve flooded zones. Deploying floating pumps allows firefighters to extract water efficiently without relying on fixed infrastructure.
Here, industrial floats are crucial. They keep pumps at optimal depths, preventing sediment intake and maintaining flow consistency. The buoyancy provided by these floats enhances mobility, allowing responders to move equipment as needed across large water surfaces.
These pump systems, supported by industrial water floats, ensure:
- Continuous water supply during firefighting operations.
- Prevention of pump clogging due to sediment or debris.
- Enhanced durability and protection of expensive equipment.
Supporting Pipe Floats for Hose and Pipeline Stability
Large-diameter hoses or temporary pipelines are often stretched across water bodies to transport water to affected areas. Without proper support, these hoses can sink, kink, or detach, severely disrupting emergency efforts.
Pipe floats prevent these issues by keeping hoses afloat and stable. They’re particularly useful in uneven terrains or dynamic water environments, ensuring steady water flow and minimizing downtime. Properly spaced pipe floats maintain hose alignment and reduce the risk of friction-related wear and tear.
When integrated with industrial water floats, the entire pipeline system gains resilience and flexibility, vital for adapting to changing conditions during emergency responses.
Role of Industrial Floats in Firefighting Scenarios
Firefighting efforts near coastal areas, riverbanks, or wetlands often rely heavily on water accessibility. In such cases, fire departments deploy floating platforms or mobile pumps that are suspended using industrial floats. These floats ensure that equipment remains above water, avoiding waterlogging and electrical short circuits.
A notable example is during wildfires that approach lakeside communities. Firefighters use floating pump stations supported by industrial floats to draw water directly from the lake. This setup ensures:
- Continuous firefighting capacity without relying on municipal hydrants.
- Strategic pump placement away from inaccessible shorelines.
- Equipment longevity through stable, dry operation.
In flood-affected areas, the quick deployment of pumps supported by industrial water floats ensures immediate drainage and mitigation efforts. These floats are engineered to support large, high-capacity pumps and offer quick assembly during time-sensitive situations.
Supporting Search and Rescue Operations
While industrial floats are widely known for their role in firefighting, they also contribute significantly to rescue missions in aquatic or flooded zones.
Search and rescue teams often navigate unstable terrain where boats or platforms are required. Modular floating docks or platforms, supported by industrial water floats, serve as:
- Launching pads for search boats.
- Resting zones for victims or responders.
- Platforms to transport medical supplies or heavy gear.
Rescue personnel often rely on pipe floats to keep communication cables or air hoses afloat, especially in submerged environments. This support is critical in maintaining safety for divers or underwater search units.
Additionally, industrial floats provide visibility and stability—two key factors that improve rescue operation outcomes during night or poor weather conditions.
Advantages of Using Industrial Floats
The adoption of industrial floats in emergency operations has grown due to their unmatched benefits. Here’s why agencies and fire departments trust them:
1. Durability
Made from UV-stabilized materials and tested against punctures, industrial floats withstand extreme environmental stress. They remain functional even after years of use in chemically harsh or salty waters.
2. Load Capacity
Modern industrial water floats can support several hundred kilograms, accommodating large pumps, equipment cases, and even personnel.
3. Easy Deployment
Time is critical during emergencies. Industrial floats offer fast assembly, modular connections, and minimal maintenance.
4. Corrosion Resistance
Since emergencies often occur in varied terrains, industrial floats are designed to resist corrosion from saltwater, oils, and chemicals.
5. Stability
Their design ensures even load distribution, reducing the risk of tipping or submerging, key during firefighting or rescue missions.
In addition, pipe floats feature easy clamping mechanisms, allowing quick integration with firefighting hoses or pipelines.
Considerations When Choosing the Right Industrial Float
Choosing the appropriate industrial floats for firefighting and emergency response operations is not as simple as picking any buoyant device. It requires a careful assessment of technical requirements, operational needs, and environmental factors. The wrong choice can lead to equipment failure, operational delays, or even life-threatening situations in high-stakes environments. Below are five key considerations to guide you in selecting the most effective industrial floats, including pipe floats and industrial water floats, for your water-based emergency setup.
1. Load and Buoyancy Requirements
The first and most crucial factor is the load-bearing capacity of the float. Every piece of equipment—whether it’s a high-capacity water pump, heavy-duty hose, generator, or modular platform—has a specific weight. The chosen industrial floats must provide enough buoyancy to support the total load with an additional safety margin. Underestimating buoyancy needs can result in submersion, instability, or even tipping during operations.
It’s important to evaluate both static and dynamic loads, especially if the floatation system will be subject to movement, vibration, or water turbulence. For firefighting pumps deployed on lakes or rivers, selecting floats with high buoyancy ratings ensures the pump intake remains at an optimal level above sediments and debris.
2. Equipment Compatibility
Not all floats are universally compatible with all types of equipment. You need to consider the shape, size, and attachment method of your current tools. Pipe floats, for instance, come in various diameters to accommodate hoses or pipelines of different sizes. A poorly fitting float may slide, shift, or detach under pressure, disrupting the water supply or causing safety hazards.
Ensure that your pipe floats have secure clamping systems, non-slip internal padding, and the proper floatation volume to keep the hose or pipe buoyant and aligned. Similarly, modular industrial floats should interlock seamlessly with your platform designs or pump bases for a secure setup.
3. Water Type and Conditions
The environment in which the floats will be deployed—saltwater, freshwater, or chemically contaminated water—plays a significant role in determining the right materials. Industrial water floats designed for saltwater use are typically built with UV-stabilized and corrosion-resistant materials to prevent degradation from saline exposure.
For operations in freshwater lakes, rivers, or reservoirs, floats made of high-density polyethylene (HDPE) with anti-algae coatings are often preferred. In industrial zones where chemical exposure is a risk, floats with reinforced coatings or specialty plastics can withstand harsh environments and maintain structural integrity over extended periods.
4. Environmental Exposure
Beyond water type, consider other environmental stresses such as UV exposure, temperature extremes, ice, or chemical runoff. Industrial floats deployed in areas with high sun exposure should be UV-resistant to prevent brittleness or fading over time.
If your operations are based in high-risk zones with industrial waste or pollutants in the water, opt for industrial water floats that include additional protection layers or internal foam cores for extra safety. Long-term exposure to chemicals can compromise the integrity of low-grade floats, leading to slow leaks or sudden failure during active use.
5. Certifications and Manufacturer Standards
Not all floats are created equal. Always source your industrial floats from reputable manufacturers who follow industry standards for safety, buoyancy, and material quality. Look for ISO certifications, field-tested performance ratings, and customer testimonials that confirm the product’s reliability under emergency conditions.
Manufacturers who specialize in emergency response equipment often offer added support, such as custom design consultations or replacement parts, which can be invaluable during critical missions. Investing in high-quality pipe floats or modular floating systems ensures consistency and performance when every second counts.
Innovations and Trends in Industrial Float Technology
The field of industrial float technology has seen remarkable advancements in recent years, driven by the increasing need for more efficient, adaptable, and environmentally responsible solutions in emergency response operations. As the challenges associated with water-based firefighting, rescue, and flood control continue to evolve, so too does the technology behind the floats that support these critical tasks. The following innovations are shaping the future of industrial float technology, making it more effective, versatile, and user-friendly in diverse emergency scenarios.
1. Eco-Friendly Materials
In response to growing concerns over environmental sustainability, many manufacturers are moving toward eco-friendly materials for constructing industrial floats. Traditionally, floats were made from materials that were durable but not always environmentally friendly. Today, there is a shift towards the use of recyclable and non-toxic materials, such as bio-based polymers and biodegradable foams, that offer similar strength and performance characteristics while reducing environmental impact. These materials are designed to withstand the harsh conditions of water environments without leaching harmful chemicals into the ecosystem. As the demand for greener technologies rises, manufacturers are increasingly integrating these eco-friendly materials into their float designs to help minimize the long-term environmental footprint of emergency operations.
2. Modular Designs
Another significant innovation in industrial float technology is the adoption of modular designs. Traditional floats were often rigid and single-purpose, limiting their flexibility in various operational contexts. Today’s advanced industrial water floats come with interlocking designs, enabling responders to quickly assemble large floating platforms or mobile workstations tailored to the specific needs of the operation. These modular systems allow for easy reconfiguration and customization, making them ideal for dynamic environments where fast changes are necessary. Modular industrial floats provide the versatility to create temporary floating bridges, platforms for heavy equipment, or expansive work zones, facilitating the rapid deployment of firefighting or rescue teams. The ability to connect multiple float units also allows for a high degree of scalability, ensuring that larger operations can be supported as the situation demands.
3. Integrated Sensors
The integration of sensors into pipe floats and pump floats represents one of the most cutting-edge advancements in float technology. These sensors monitor various parameters such as tilt, water levels, and structural integrity in real-time, allowing operators to track the condition of critical equipment remotely. This innovation provides valuable insights into the performance and stability of floating platforms, ensuring they remain safely afloat during operations. For example, sensors can alert emergency teams if a float is tilting too much, signaling that it may become unstable or submerged. Similarly, water level sensors can help adjust equipment positioning automatically to maintain optimal buoyancy. The real-time data collected by these sensors can be transmitted to central command units, enhancing decision-making and improving the overall efficiency of operations. This technology enhances both safety and performance, particularly in challenging and rapidly changing water environments.
4. Collapsible Floats
For areas where space and storage are limited, collapsible industrial floats have emerged as a game-changing innovation. These floats are designed to collapse into compact, space-saving units for easy transportation and storage. Once on-site, they can be rapidly deployed, inflating or expanding to their full size within minutes. Collapsible industrial floats are especially useful in situations where rapid response times are crucial, such as during floods or fires in remote areas. The lightweight and space-efficient design allows for faster transportation, making it possible to quickly set up floating platforms, pump stations, or hoses in areas that would otherwise be difficult to access. This innovation dramatically reduces the logistical challenges associated with transporting and deploying traditional float systems, allowing for quicker response times and greater operational flexibility.
Conclusion
In the complex and unpredictable world of emergency response, industrial floats are more than just accessories—they are essential tools that enhance the effectiveness of firefighting and rescue missions. Whether it’s floating high-capacity pumps, supporting long water pipelines, or stabilizing rescue platforms, the importance of reliable buoyancy solutions cannot be overstated.
From pipe floats keeping hoses secure to rugged industrial water floats providing unwavering support, the right floating solutions ensure safety, speed, and success in the most challenging conditions.
For agencies seeking dependable solutions, investing in high-quality industrial floats is a step toward resilience and readiness. In life-threatening situations, every second matters—and every piece of equipment, especially those that float, must perform flawlessly.
Have Questions?
Get in touch with us now!
Related Blogs
Advancements in Dredging Technology: Automation, GPS, and Real-Time Monitoring
Selecting the right dredging machine is one of the most important decisions a contractor or operator will make in the lifecycle of a dredging project. Whether the goal is land reclamation, port expansion, reservoir desilting, or mining operations, the equipment you choose plays a crucial role in determining operational success, environmental compliance, and overall cost efficiency.
Key Engineering Considerations for Installing Irrigation Pipe Floats in Uneven Terrain
Selecting the right dredging machine is one of the most important decisions a contractor or operator will make in the lifecycle of a dredging project. Whether the goal is land reclamation, port expansion, reservoir desilting, or mining operations, the equipment you choose plays a crucial role in determining operational success, environmental compliance, and overall cost efficiency.
Choosing the Right Dredging Machine: A Complete Buyer’s Guide for Contractors and Operators
Selecting the right dredging machine is one of the most important decisions a contractor or operator will make in the lifecycle of a dredging project. Whether the goal is land reclamation, port expansion, reservoir desilting, or mining operations, the equipment you choose plays a crucial role in determining operational success, environmental compliance, and overall cost efficiency.