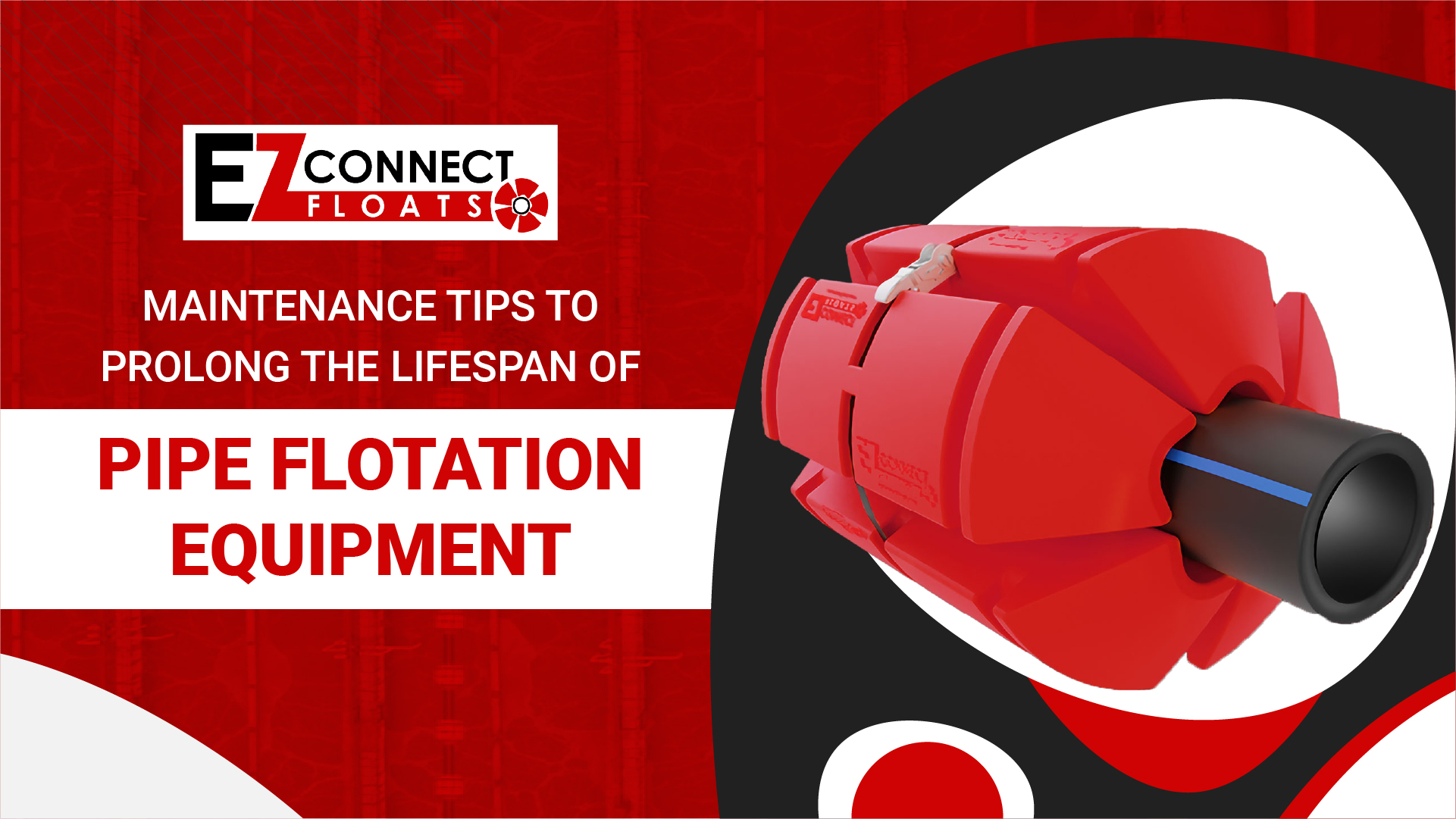
Maintenance Tips for Pipe Flotation Equipment
Maintenance Tips to Prolong the Lifespan of Pipe Flotation Equipment
Pipe flotation equipment plays a vital role in various industries by ensuring that pipes, cables, and other critical infrastructure stay buoyant and remain in place, especially in water or underwater environments. Whether used in the oil and gas sector for pipeline installation, marine construction for laying underwater cables, or water distribution systems, the performance and reliability of pipe flotation systems are essential for the success of projects and the efficiency of operations. A well-maintained flotation system not only improves operational efficiency but also reduces costs, extends the lifespan of equipment, and ensures compliance with safety regulations.
Pipe flotation equipment typically consists of buoyant components, such as pipe floats and flotation collars, designed to keep pipes or other submerged infrastructure afloat until they are positioned in their final location. The durability and functionality of these flotation devices are directly impacted by environmental factors like UV exposure, salt water, and extreme weather conditions. Over time, these conditions can cause wear and tear on the equipment, leading to reduced performance, system failures, or even costly repairs. Proper maintenance is, therefore, crucial to prevent such issues and keep the system operating smoothly.
In this article, we will explore practical maintenance tips to ensure the longevity and consistent performance of pipe flotation equipment. By following these guidelines, industries can reduce downtime, prevent unexpected failures, and avoid costly repairs or replacements.
Why Maintenance Matters
Regular maintenance helps to identify potential problems before they escalate. Issues like cracks, corrosion, or material degradation can severely impact the effectiveness of pipe flotation systems. The longer these problems go unchecked, the more costly and complex the repairs can become. Routine care, including regular inspections and cleaning, ensures that the equipment remains in good working condition, thus preventing operational disruptions and extending its service life.
1. Understanding Pipe Flotation Equipment
To fully appreciate the importance of proper maintenance, it’s essential to understand what pipe flotation equipment is, how it works, and where it’s used.
What Is Pipe Flotation? Pipe flotation refers to the process by which pipes are kept afloat on water bodies or buoyed above the seabed during construction or installation. This process typically involves the use of pipe floats or flotation collars that are attached to the pipe, enabling it to remain buoyant until it’s placed in its final position.
Key Components of Pipe Flotation Equipment
- Pipe Floats: These are the main buoyant structures attached to the pipe to provide buoyancy. They are designed to float on water, lifting pipes off the seabed or water surface.
- Flotation Collars: Collars are typically cylindrical devices that surround the pipe and are used in conjunction with pipe floats to improve stability and control.
- Attachment Points: These are the connectors that attach the pipe floats or flotation collars to the pipe. Ensuring these points are securely fixed is critical to the system’s performance.
Common Applications Pipe flotation equipment is widely used in industries such as:
- Oil and Gas: For laying underwater pipelines that transport oil, gas, and other fluids across vast distances.
- Marine and Coastal Construction: Used in the installation of infrastructure like underwater cables, pipelines, and support structures for offshore platforms.
- Water Distribution: In large-scale irrigation or water supply systems, pipe flotation helps position pipes in water bodies for easy access and maintenance.
By keeping these components in top condition, industries can avoid unexpected failures, reduce downtime, and ensure that operations continue smoothly.
2. Regular Inspections: The First Line of Defense
The first step in maintaining pipe flotation equipment is performing regular inspections. Frequent checks help detect wear and tear before it leads to more significant issues, allowing you to replace or repair components as needed.
Importance of Periodic Inspections Regular inspections allow you to spot damage, corrosion, and other issues early, which can prevent costly repairs and downtime in the future. Many problems with pipe flotation systems arise from unnoticed small issues that escalate over time. Thus, routine checks are the foundation of effective maintenance.
What to Inspect
- Pipe Floats: Check for any signs of cracks, wear, or damage to the outer surface of the pipe floats. Since these components are often exposed to harsh environmental conditions, they are susceptible to degradation over time.
- Floatation Collars: Ensure that flotation collars are intact and not experiencing any deformation or signs of fatigue. Deformation can result in reduced buoyancy and stability, which could cause improper installation or drifting.
- Attachment Points: Inspect the attachment points for signs of corrosion, rust, or loosening. These are critical areas that ensure that the floats remain securely attached to the pipe.
- Buoyancy Materials: For foam-filled floats, check for leaks or punctures that could cause the foam to lose buoyancy.
Signs of Damage to Watch For
- Cracks or chips in the pipe float material.
- Deformation or bending of flotation collars.
- Rust or corrosion on metallic components.
- Evidence of material breakdown from UV exposure or harsh weather.
- Detachment of floats or collars from the pipe.
Inspection Frequency The frequency of inspections depends on the specific environment and the usage of the equipment. For instance:
- In marine environments where saltwater and harsh weather conditions prevail, more frequent inspections (e.g., every 3 to 6 months) may be necessary.
- For pipe floats in less severe conditions, inspections every 6 to 12 months may suffice.
3. Cleaning and Maintenance Routine
Routine cleaning and upkeep of your pipe flotation equipment are crucial to preventing damage caused by environmental exposure. Whether the system is in use or not, cleaning helps maintain its structural integrity.
Importance of Cleaning Over time, dirt, algae, salt, and other debris can accumulate on pipe flotation systems, leading to potential corrosion or blockage. Left untreated, these buildups can degrade the materials and reduce the effectiveness of the flotation devices.
Cleaning Recommendations
- Freshwater Rinse: After each use in saltwater, rinse pipe floats and collars with fresh water to remove salt, debris, and other contaminants. This helps prevent corrosion and material degradation.
- Scrub and Detach Debris: Use non-abrasive scrubbers or brushes to remove stubborn algae or mineral deposits that may have adhered to the floats. Avoid harsh chemicals that could damage the flotation material.
- Inspect as You Clean: During cleaning, it’s the perfect opportunity to check for signs of damage or wear. Thoroughly inspect the equipment as you clean, particularly in hard-to-reach areas like attachment points.
Cleaning Frequency
- In marine environments, where exposure to salt and algae is frequent, cleaning may be needed every few weeks, especially if the equipment is in constant use.
- In freshwater environments or less exposed conditions, cleaning can be done less frequently, such as once every 6 to 12 months, depending on usage.
4. Protecting Against Environmental Wear
Pipe flotation equipment is constantly exposed to varying environmental conditions, from UV rays to salty water to extreme temperatures. These factors can degrade materials over time, reducing their effectiveness and lifespan. Taking steps to protect against environmental wear is key to prolonging the life of pipe flotation systems.
Impact of UV Exposure and Saltwater
- UV Radiation: Continuous exposure to UV rays can cause plastic and rubber components to crack, discolor, or degrade. Materials that are not UV-resistant may lose their flexibility or strength, which could compromise the buoyancy and safety of the equipment.
- Saltwater: Salt can accelerate the corrosion of metal components, leading to rust and eventual failure of the flotation system. This is particularly true in harsh marine environments.
Protective Measures
- UV-Resistant Materials: When selecting pipe floats, choose those made from UV-resistant materials. Polyethylene and other durable plastics with UV stabilizers can significantly extend the lifespan of flotation devices.
- Anti-Corrosion Coatings: Use coatings designed to prevent rust and corrosion on metallic components. Zinc or epoxy-based coatings can be effective for preventing corrosion in saltwater environments.
- Protective Covers: When the equipment is not in use, consider using protective covers to shield it from prolonged UV exposure and environmental contaminants. This is particularly important for equipment that is stored outside or in exposed locations.
5. Lubrication and Anti-Corrosion Measures
Although flotation equipment is designed to float, there may be parts that involve mechanical movement or connections, such as anchors or joints. Regular lubrication and anti-corrosion treatments for these components are essential to keep them functioning properly.
Importance of Lubrication Lubricating moving parts ensures that they move freely and do not get stuck due to friction or the buildup of corrosion. Regular lubrication helps prevent mechanical failures that can lead to costly downtime or equipment replacements.
Anti-Corrosion Treatments In addition to lubrication, it is essential to treat metal components with anti-corrosion coatings. These coatings provide a protective layer against saltwater, moisture, and other environmental factors that can accelerate the oxidation of metals. Depending on the material, common anti-corrosion treatments include:
- Zinc coatings (for steel components).
- Epoxy coatings for enhanced durability.
- Galvanizing for long-term protection against rust.
Recommended Lubricants: When choosing lubricants, make sure they are compatible with the materials used in your pipe flotation equipment. Silicone-based lubricants are a common choice, as they can protect against moisture while providing a long-lasting, non-greasy finish.
6. Load Management and Proper Installation
Improper load management and installation are common causes of premature wear and failure in pipe flotation systems. Ensuring that the equipment is installed correctly and operated within its load capacity is vital for longevity.
Overloading and Improper Installation: When pipe flotation systems are subjected to excessive weight or installed improperly, they may not perform optimally, leading to uneven buoyancy or structural damage. Overloading can also stress the attachment points, causing them to loosen or fail.
Using a Pipe Flotation Calculator: A pipe flotation calculator is an invaluable tool for ensuring that the right number and type of pipe floats are used for a given pipe size and weight. Pipe flotation refers to the method used to keep pipes, cables, or other infrastructure buoyant on water until they are positioned at the intended location. By calculating the buoyancy required to support the pipe, operators can avoid overloading the system and ensure that the flotation equipment operates efficiently.
Best Installation Practices
- Ensure that the pipe floats and flotation collars are securely attached to the pipe at the correct intervals.
- Use the appropriate type and number of floats based on the weight and size of the pipe.
- Install the equipment in a manner that evenly distributes the load, preventing undue stress on any individual component.
7. Storage Tips for Longevity
When pipe flotation equipment is not in use, proper storage is essential to prevent environmental damage and degradation. Storing flotation equipment correctly can significantly prolong its lifespan.
Ideal Storage Conditions
- Dry and Cool Place: Store pipe flotation equipment in a dry, cool location away from direct sunlight. Avoid exposure to UV rays and extreme temperatures that can cause materials to break down.
- Avoid Contact with Rough Surfaces: When storing floats, ensure that they are not in direct contact with rough surfaces that could cause scratches or punctures. If possible, store them on soft, padded surfaces to prevent damage.
8. Replacement and Upgrading
Even with diligent maintenance, there comes a time when pipe flotation equipment needs to be replaced or upgraded. Monitoring the performance of the equipment and recognizing when it’s time for a change can prevent costly failures.
Signs It’s Time to Replace
- Significant damage to pipe floats or collars that can’t be repaired.
- Diminished buoyancy due to internal damage or leaks.
- Extensive corrosion or material degradation that compromises safety.
Upgrading Equipment Upgrading to more advanced, durable materials can extend the lifespan of your pipe flotation systems. Consider newer materials with improved UV resistance or more advanced anti-corrosion features for better performance in extreme environments.
Conclusion
Maintaining pipe flotation equipment is crucial for ensuring that it continues to perform reliably and safely throughout its lifespan. By following a regular maintenance schedule that includes inspections, cleaning, protecting against environmental wear, and using the right tools and lubricants, you can significantly extend the life of your flotation systems.
Remember that proper installation and load management are equally important in preventing unnecessary strain on the equipment. And when the time comes, replacing or upgrading components ensures that your pipe flotation system remains efficient and dependable for years to come. Through proactive maintenance, industries can ensure operational efficiency, reduce costs, and prevent system failures, ultimately protecting both equipment and the investment they represent.
Have Questions?
Get in touch with us now!
Related Blogs
Key Components of an HDPE Fusion Machine and Their Functions Explained
Introduction Understanding the HDPE Fusion Machine Key Components of an HDPE Fusion Machine How HDPE Fusion Works: From Setup to Solid Joint Performance and ROI
Advancements in Dredging Technology: Automation, GPS, and Real-Time Monitoring
Introduction What Is Modern Dredging Technology? Core Technological Advances Reshaping Dredging Application Benefits Across Key Industries Remote Operations and Cloud Connectivity Sustainability and Compliance Built
Key Engineering Considerations for Installing Irrigation Pipe Floats in Uneven Terrain
Introduction Purpose of Irrigation Pipe Floats Engineering Challenges in Uneven Terrain Design and Installation Considerations Addressing Common Mistakes in Irrigation System Installation Performance Benefits of