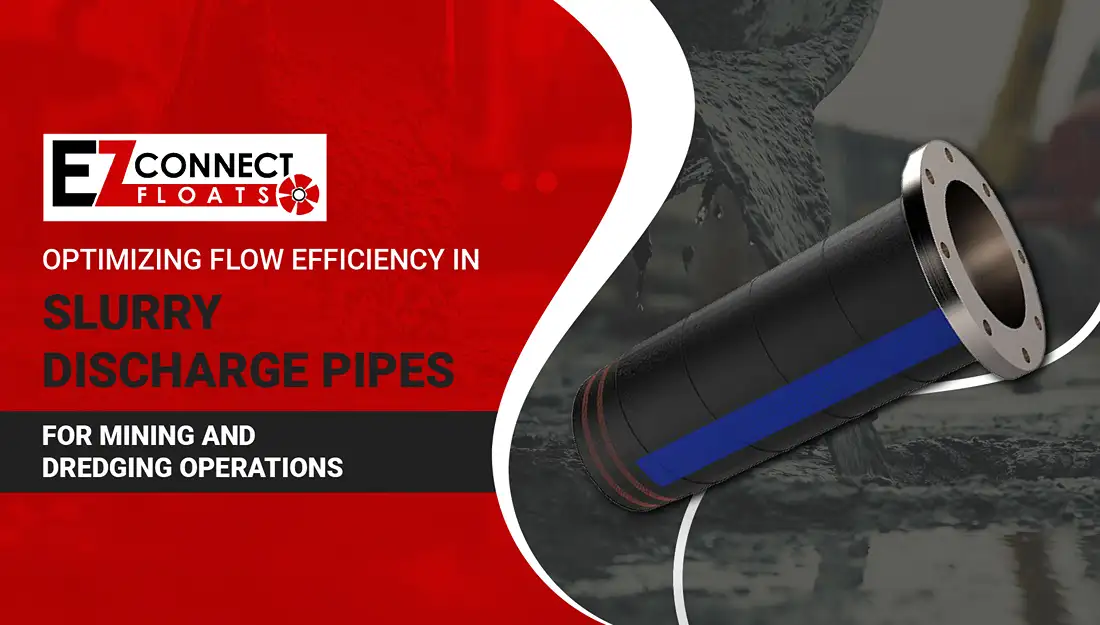
Optimizing Flow Efficiency in Slurry Discharge Pipes
In mining and dredging operations, efficient slurry transport is essential for maintaining high productivity, minimizing operational costs, and avoiding unnecessary downtime. The slurry discharge pipe and slurry fill pipe are both crucial components that ensure the smooth transfer of slurry from one point to another, whether it’s for waste removal in mining or dredging sediment from waterways. Optimizing the flow efficiency in both the slurry discharge pipe and slurry fill pipe is key to achieving optimal performance, reducing wear and tear, and extending the lifespan of the equipment.
This article delves into the importance of optimizing the flow efficiency of slurry discharge pipe, highlighting best practices in design, material selection, maintenance, and advanced technologies that contribute to achieving efficient slurry transport.
- Understanding Slurry Discharge Pipe
- Key Factors Affecting Flow Efficiency in Slurry Discharge Pipe
- Best Practices for Designing Slurry Discharge Pipe
- Maintaining Slurry Discharge Pipe for Maximum Efficiency
- The Role of Slurry Hoses in Dredging and Mining Operations
- Advanced Technologies for Optimizing Slurry Discharge Pipe Flow
- Conclusion
- Understanding Slurry Discharge Pipe
- Key Factors Affecting Flow Efficiency in Slurry Discharge Pipe
- Best Practices for Designing Slurry Discharge Pipe
- Maintaining Slurry Discharge Pipe for Maximum Efficiency
- The Role of Slurry Hoses in Dredging and Mining Operations
- Advanced Technologies for Optimizing Slurry Discharge Pipe Flow
- Conclusion
Understanding Slurry Discharge Pipe
A slurry discharge pipe is a crucial component in any mining or dredging operation where materials such as water, sand, mud, and other solid particles are transported in a semi-liquid state. These pipes carry the slurry from processing or dredging equipment to settling ponds, treatment plants, or designated discharge points. A slurry discharge pipe must handle the abrasive nature of the materials they carry, along with the pressure and flow variations that occur during operation.
In addition to a slurry discharge pipe, you may encounter slurry fill pipe and slurry hose. While a slurry discharge pipe transports the waste slurry to a final location, a slurry fill pipe is used for introducing slurry into certain systems or tanks. Slurry hoses, on the other hand, are flexible alternatives to rigid pipes and are often used when flexibility and ease of handling are necessary, especially in dynamic, hard-to-reach locations like dredging operations.
Optimizing the flow efficiency of these systems ensures minimal energy consumption, reduces the need for frequent maintenance, and enhances the overall productivity of operations.
Key Factors Affecting Flow Efficiency in Slurry Discharge Pipe
Several factors influence the efficiency of slurry flow through the discharge pipe. These factors must be considered carefully during the design phase and throughout the life of the system to ensure that the slurry moves through the pipes without unnecessary resistance, friction, or blockages.
1. Pipe Design
The design of the slurry discharge pipe is one of the most significant factors in optimizing flow efficiency. Pipe diameter, pipe length, and the number of bends or turns in the system all directly affect how smoothly the slurry can flow through the pipes.
- Pipe Diameter: Larger diameter pipes reduce the velocity of the slurry, which can reduce wear and tear, but may also increase the energy required to move the slurry. On the other hand, smaller diameter pipes increase the flow velocity, which can lead to excessive wear and the potential for pipe blockages. It’s crucial to find a balance in the design of the pipe diameter to optimize flow rates without increasing energy consumption or pipe maintenance.
- Pipe Length and Bends: Longer pipes and more bends cause more friction and resistance, which reduces flow efficiency. Keeping the distance the slurry travels as short as possible and minimizing the number of bends will reduce energy consumption and wear. In some cases, installing straight pipes with fewer directional changes will result in better flow dynamics.
2. Type of Material Used
The material selected for slurry discharge pipe is crucial to their longevity and performance. Slurry can be abrasive and corrosive, and the wrong pipe material will wear out quickly, leading to higher replacement costs and reduced flow efficiency.
- Metal Pipes: Metal pipes, particularly steel, are durable and able to handle high pressures and rough slurry. However, metal pipes may be prone to corrosion over time, especially when exposed to certain chemicals in the slurry.
- Rubber Linings: Rubber-lined pipes offer enhanced resistance to wear and are ideal for handling highly abrasive slurries. These linings help reduce the impact of abrasive particles and extend the life of the pipe.
- HDPE Pipes: High-density polyethylene (HDPE) pipes are lightweight, corrosion-resistant, and flexible. They are an excellent choice for applications where there is a need for flexible and durable slurry discharge pipe.
Selecting the proper material for your slurry discharge pipe will ensure that your system is not only efficient but also cost-effective in the long term.
3. Slurry Characteristics
The type of slurry being transported also plays a significant role in optimizing flow efficiency in the slurry discharge pipe. The viscosity and density of the slurry determine the resistance encountered as it moves through the pipe. Higher-density slurry will require more energy to pump, which can affect the flow rates and increase the risk of blockages within the slurry discharge pipe. Managing these factors is essential to maintaining efficient transport and preventing unnecessary wear or downtime.
Proper understanding of the slurry characteristics helps in designing the system to handle the specific flow behavior of the material. In some cases, additives may be used to improve flowability and reduce the chances of clogs or excessive wear.
4. Flow Velocity and Pressure
Maintaining an optimal flow velocity within the slurry discharge pipe is crucial. High velocity leads to wear and tear, while low velocity increases the risk of settling solids and clogging. The optimal velocity depends on the type of slurry and the pipe’s design. It’s important to maintain a consistent flow velocity that prevents the solids from settling while avoiding excessive friction and wear.
Along with flow velocity, pressure also plays a role in optimizing flow efficiency. The pressure within the pipe should be monitored and controlled to avoid fluctuations that could result in blockages or pipeline ruptures.
Best Practices for Designing Slurry Discharge Pipe
Designing an efficient slurry discharge system requires careful consideration of several factors. Below are some best practices for optimizing the performance of your slurry discharge pipe.
1. Optimize Pipe Sizing
Proper sizing of the slurry discharge pipe is essential to ensuring optimal flow rates and energy consumption. Pipes that are too small can cause the slurry to flow too quickly, increasing friction and wear. Similarly, pipes that are too large can reduce the velocity, making it more difficult to maintain adequate flow. It’s important to work with engineers to determine the optimal pipe size based on the slurry characteristics and system requirements.
2. Material Selection for Durability
Choosing the right material for your slurry discharge pipe will help reduce wear and tear, increase longevity, and prevent unexpected downtimes. Using wear-resistant materials, such as rubber linings or HDPE, is crucial in abrasive environments. Additionally, pipes should be selected based on their resistance to corrosion, pressure, and temperature fluctuations to ensure durability under varying operating conditions.
3. Proper Slope and Alignment
For gravity-fed systems, the pipe’s slope and alignment are crucial to maintaining efficient flow. Pipes should be installed at the correct angle to encourage the natural movement of slurry without requiring additional pumping power. Avoiding sharp bends and designing a smooth path for the slurry will reduce resistance and improve flow efficiency.
4. Minimize Pipe Friction
Friction loss in the slurry discharge pipe system can be minimized by selecting the proper pipe material, keeping the pipe’s surface smooth, and ensuring that bends are gradual. The smoother the interior surface of the pipe, the less friction will occur, allowing slurry to move more easily.
Maintaining Slurry Discharge Pipe for Maximum Efficiency
Ensuring the longevity and optimal performance of slurry discharge pipe is crucial for smooth operations in mining and dredging activities. Regular maintenance helps prevent costly repairs, reduces downtime, and ensures that slurry flows efficiently through the pipes. Without proper upkeep, issues such as blockages, excessive wear, and corrosion can severely impact the efficiency of the system, leading to delays and increased operational costs. Below are several key maintenance strategies that can help maintain the performance of slurry discharge pipe over time.
1. Regular Inspections and Cleaning
One of the most fundamental maintenance practices is conducting regular inspections of the slurry discharge pipe system. These inspections should be done frequently to detect early signs of potential problems such as wear, corrosion, or damage. Even the smallest crack or wear spot can lead to bigger issues down the line, so addressing such problems promptly is vital to avoiding costly repairs or system shutdowns.
Along with inspections, regular cleaning is also essential. Slurry, by its very nature, can contain various types of solids and abrasive particles that may build up over time and restrict flow. Inadequate cleaning can result in a buildup of material inside the pipe, leading to reduced flow rates, increased pressure, and a greater risk of clogging. Regularly scheduled cleanings will ensure that the pipes remain clear and free of blockages, allowing the slurry to flow smoothly. Cleaning can be done using high-pressure water jets or other mechanical methods depending on the type of slurry being transported.
2. Wear Monitoring
Slurry discharge pipe is constantly subject to wear, particularly in areas where the flow velocity is high or where there are bends or joints. The abrasive nature of many slurries accelerates pipe degradation, causing the material to thin over time, which weakens the pipe structure. These vulnerable areas should be monitored regularly to detect early signs of wear.
Special attention should be paid to bends in the pipe, as these areas often experience higher levels of friction and wear. Joints are another common weak point, where stress can cause cracks to form over time. Early identification of these areas can prevent further damage and costly repairs. Technologies such as wear monitoring sensors, or periodic thickness testing, can be employed to help identify when specific sections of the slurry discharge pipe need repair or replacement.
In some cases, proactive maintenance involves replacing worn-out sections before they lead to failure. By replacing these parts on a schedule based on wear monitoring, operations can avoid unexpected downtime or catastrophic pipe bursts. Additionally, some advanced materials or rubber linings can be added to protect high-wear sections, which can help extend the lifespan of the entire system.
3. Managing Slurry Composition
The composition of the slurry being transported plays a significant role in maintaining the efficiency of the discharge pipes. Slurries that are too thick or have a high concentration of solids can increase the risk of blockages, reduce flow efficiency, and cause significant wear on the pipes. Therefore, it’s essential to manage the consistency of the slurry being pumped through the system to minimize potential issues.
One way to manage slurry composition is by removing excess water before it enters the pipe system. This can be done using dewatering processes or separating excess liquid from the solids. Reducing the amount of solid material in the slurry will not only help in improving flow efficiency but will also reduce the pressure on the discharge pipes, resulting in less wear.
Furthermore, if possible, reduce the concentration of abrasive solids. Some slurries, especially those in mining operations, can contain highly abrasive materials that significantly contribute to pipe erosion. Monitoring the types of solids being transported can help reduce wear and extend the life of the slurry discharge pipe. In cases where abrasive content is unavoidable, it may be beneficial to use pipes with abrasion-resistant linings or materials, such as rubber-coated pipes or HDPE (high-density polyethylene) pipes, to withstand the wear.
The Role of Slurry Hoses in Dredging and Mining Operations
In certain situations, slurry hoses are used instead of a traditional slurry discharge pipe. These hoses are flexible and can be easily maneuvered in tight spaces, making them ideal for dynamic and hard-to-reach areas like dredging sites.
While slurry discharge pipe is often used in fixed, permanent systems, slurry hoses provide the flexibility needed for applications where pipes cannot be laid out in a straight line. The main advantage of slurry hoses is their ease of transport, but they must also be maintained to prevent damage from abrasives or pressure fluctuations.
Advanced Technologies for Optimizing Slurry Discharge Pipe Flow
Advancements in technology have led to significant improvements in slurry discharge systems. Real-time sensors and monitoring systems can track the performance of the slurry discharge pipe, allowing operators to make adjustments before issues arise. Automated control systems can also regulate pressure and flow, ensuring consistent operation and reducing the need for manual intervention.
Moreover, the development of advanced pipe linings and materials has made slurry discharge pipe more durable, reducing the frequency of maintenance and improving flow efficiency.
Conclusion
Optimizing the flow efficiency of slurry discharge pipe and slurry fill pipe is crucial for reducing operational costs, minimizing downtime, and enhancing the longevity of mining and dredging operations. By prioritizing effective design, material selection, proper maintenance, and incorporating advanced technologies, companies can ensure smooth and efficient slurry transport systems. Key factors such as pipe diameter, material choice, flow velocity, pressure, and the proper use of slurry fill pipe all contribute to creating a system that reduces friction, wear, and energy consumption while boosting overall productivity. Thoughtful integration of these elements leads to long-term efficiency and reduced operational costs.
Have Questions?
Get in touch with us now!
Related Blogs
Advancements in Dredging Technology: Automation, GPS, and Real-Time Monitoring
Selecting the right dredging machine is one of the most important decisions a contractor or operator will make in the lifecycle of a dredging project. Whether the goal is land reclamation, port expansion, reservoir desilting, or mining operations, the equipment you choose plays a crucial role in determining operational success, environmental compliance, and overall cost efficiency.
Key Engineering Considerations for Installing Irrigation Pipe Floats in Uneven Terrain
Selecting the right dredging machine is one of the most important decisions a contractor or operator will make in the lifecycle of a dredging project. Whether the goal is land reclamation, port expansion, reservoir desilting, or mining operations, the equipment you choose plays a crucial role in determining operational success, environmental compliance, and overall cost efficiency.
Choosing the Right Dredging Machine: A Complete Buyer’s Guide for Contractors and Operators
Selecting the right dredging machine is one of the most important decisions a contractor or operator will make in the lifecycle of a dredging project. Whether the goal is land reclamation, port expansion, reservoir desilting, or mining operations, the equipment you choose plays a crucial role in determining operational success, environmental compliance, and overall cost efficiency.