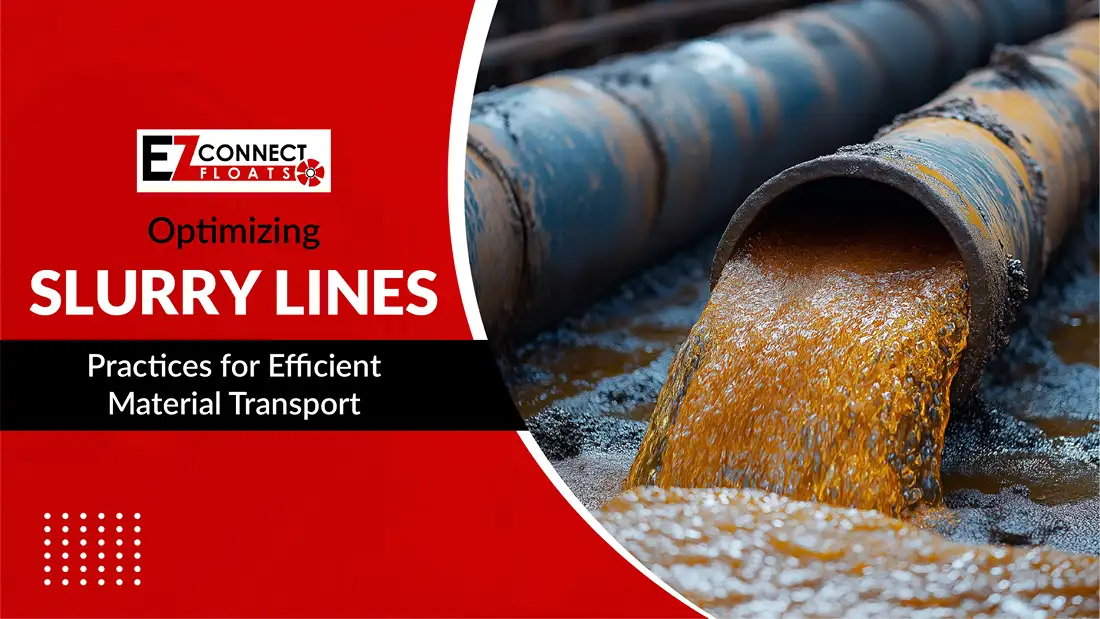
Efficient Slurry Lines Optimization Tips
Introduction
Slurry lines are a critical component in a variety of industries, including mining, wastewater treatment, and chemical processing. These lines transport a mixture of solids and liquids, also known as slurry, through pipelines from one location to another. The effectiveness of slurry lines directly impacts the efficiency and performance of the entire system. However, managing slurry transport effectively can be challenging due to the nature of the materials involved. Slurries are often abrasive, corrosive, and heavy, which can result in increased wear and tear, blockages, and inefficient material transport.
To address these challenges, optimizing them is essential for improving system performance, reducing downtime, and enhancing overall efficiency. This blog outlines some of the best practices for optimizing slurry lines to ensure smooth material transport and extend the lifespan of your infrastructure.
Understanding Slurry Lines
Before diving into optimization strategies, it’s important to understand the fundamental aspects of slurry lines and their role in industrial processes.
What Are Slurry Lines?
Slurry lines are pipelines designed to carry slurries, which are mixtures of solid particles suspended in a liquid. These mixtures can range from fine powders to coarse particles, depending on the specific application. The slurry can be water-based or involve other liquids, such as chemicals, oils, or solvents. The design and construction of slurry lines must account for the nature of the slurry, ensuring that the pipeline can handle the unique challenges presented by the transported materials.
Types of Slurry Lines
They come in various types, each designed to cater to specific applications and the properties of the slurries they transport. The choice of slurry line material depends largely on factors like the abrasiveness, corrosiveness, and flow conditions of the slurry.
1. Mild Steel Slurry Lines
Mild steel slurry lines are one of the most commonly used types of slurry pipelines. These lines are generally cost-effective and can handle a variety of slurries, especially those with lower abrasiveness. However, they are susceptible to corrosion and wear, particularly in harsh environments. When transporting slurries that contain corrosive chemicals or particles that can cause erosion, mild steel lines may degrade over time, leading to higher maintenance costs. Mild steel slurry lines are best suited for applications where slurry composition is relatively non-abrasive and the operating conditions are less demanding.
2. Composite Slurry Lines
Composite slurry lines offer superior resistance to corrosion and wear compared to mild steel lines. These pipes are made from materials that combine the benefits of different substances, such as fiberglass and resin, making them both durable and lightweight. Composite slurry lines are ideal for slurries that are more aggressive or corrosive, as they provide enhanced protection against erosion. While these lines tend to be more expensive than mild steel options, their durability and longevity make them a cost-effective choice in the long run, particularly in industries like mining and wastewater treatment.
3. Lined Slurry Lines
Lined slurry lines are equipped with a protective lining made from materials such as rubber, ceramic, or plastic. This lining serves as a barrier to prevent wear and corrosion caused by abrasive and aggressive slurries. Lined slurry pumps and pipes are particularly beneficial for industries where the slurry contains hard particles, such as in mining, cement production, and chemical processing. The linings provide added protection to the pipeline, extending its lifespan and reducing maintenance costs. While lined slurry lines can be more expensive upfront, their durability and efficiency make them a preferred choice for handling abrasive slurries.
Common Applications of Slurry Lines
They are used in various industries, including:
- Mining: To transport mined ore and tailings.
- Water Treatment: For transporting sludge and other waste materials.
- Cement Industry: For transporting raw materials like cement slurry.
- Chemical Processing: For transporting slurry materials used in chemical reactions.
The right slurry line system is critical to maintaining efficiency and preventing costly downtime caused by blockages or wear.
Key Factors Influencing Slurry Line Performance
Several factors influence their performance, including the type of slurry, pipe material, flow conditions, and system maintenance. Understanding these factors can help optimize slurry lines for maximum efficiency.
Slurry Properties
The properties of the slurry being transported can significantly affect the performance of slurry lines. Two key properties to consider are viscosity and particle size.
- Viscosity and Density: Thicker slurries require more energy to pump through pipelines. The viscosity of the slurry affects the flow rate and the amount of pressure required to keep it moving. Higher viscosity slurries tend to cause more wear on the pipes and pumps, while lower viscosity slurries can flow more easily but may require more frequent maintenance.
- Particle Size and Abrasiveness: Larger, more abrasive particles can cause significant wear on slurry lines. These particles can lead to erosion and abrasion inside the pipeline, especially if the slurry line is not lined with appropriate materials. This is why lined slurry pumps and pipes are essential for applications involving coarse or sharp particles.
Pipe Material Selection
The material chosen for the slurry line is critical to ensuring long-term performance. Several materials are commonly used in slurry lines:
- Mild Steel: While less expensive, mild steel is prone to corrosion and wear over time, especially when transporting abrasive or corrosive slurries.
- Rubber Lining: Rubber linings are often used to reduce wear from abrasive slurries. They provide a smooth surface that can minimize friction and prevent corrosion.
- Ceramic Lining: Ceramic is highly resistant to abrasion, making it an ideal choice for slurry lines transporting materials like sand, coal, and other abrasive substances.
- Composite Materials: These materials combine the benefits of rubber and ceramic, offering excellent resistance to both abrasion and corrosion.
Flow Rate and Velocity
The flow rate and velocity of slurry lines are essential to their performance. Slurry lines that are too small or too large for a given flow rate may experience issues such as clogging, settling, or excessive wear. Maintaining the optimal velocity ensures that the slurry stays suspended and flows smoothly without causing blockages. High flow rates can reduce the risk of settling, but they may also increase wear on the pipes. On the other hand, low flow rates may cause particles to settle, leading to blockages or inefficient transport.
Best Practices for Optimizing Slurry Lines
To ensure that they operate efficiently and effectively, several best practices can be implemented. These practices focus on reducing wear, preventing blockages, and optimizing flow conditions.
1. Selecting the Right Pipe Material
One of the first steps in optimizing them is choosing the appropriate pipe material. For slurries with high abrasiveness, lined slurry pumps and pipes are the most effective solution. These linings protect the pipeline from erosion and corrosion while maintaining smooth flow. For less abrasive slurries, composite or mild steel pipes may be sufficient.
When choosing materials for slurry lines, consider the following factors:
- The type of slurry being transported.
- The expected wear rate on the pipes.
- The need for corrosion resistance.
- The cost of the materials.
Lined slurry pumps, in particular, offer excellent protection for slurry lines that transport abrasive materials, extending the lifespan of the entire system.
2. Regular Inspection and Maintenance
Routine inspection and maintenance are crucial to optimizing slurry lines. Over time, they may experience wear, clogging, or buildup, which can decrease their efficiency. Regular checks can identify potential problems early, preventing costly downtime.
Some essential maintenance practices include:
- Inspecting for Corrosion and Wear: Look for signs of corrosion, pitting, and erosion, especially in areas of high wear.
- Cleaning the System: Regular cleaning can prevent clogging and ensure smooth flow.
- Replacing Worn Components: If parts of the slurry line, including pumps and valves, show signs of wear, replace them before they fail.
3. Optimizing Pump and Valve Systems
The pumps and valves used in slurry lines play a significant role in maintaining flow efficiency. Choosing the right lined slurry pump for a given application can minimize energy consumption and reduce the risk of blockages. A properly selected slurry pump will handle the flow rate and pressure needed for optimal slurry transport.
Consider the following tips for optimizing pump and valve systems:
- Use pumps that are appropriately sized for the expected flow rate and pressure.
- Ensure that valves are correctly set to control the flow of slurry without causing backpressure or blockages.
- Regularly check pump seals and valves for signs of wear or damage.
4. Monitoring Slurry Flow Conditions
Monitoring the flow conditions of them is essential for ensuring they remain optimized. Modern flow meters and sensors can be used to track key parameters such as pressure, temperature, and flow rate. By monitoring these variables in real-time, you can detect any issues early and make adjustments as necessary.
Automated systems that provide continuous monitoring can alert operators to changes in the flow, enabling proactive maintenance and minimizing the risk of system failure.
5. Proper Pipeline Design
The design of them is crucial to optimizing their performance. Well-designed pipelines ensure that the slurry flows smoothly without causing excessive wear or blockages. Some key considerations for pipeline design include:
- Pipe Diameter: The diameter should be large enough to prevent excessive friction and ensure the slurry flows freely.
- Pipe Slope: A gentle slope is ideal for maintaining the momentum of the slurry and preventing sedimentation.
- Bends and Turns: Minimizing the number of bends and turns in the pipeline helps maintain flow velocity and reduces the risk of blockages.
A properly designed slurry line system ensures that the materials are transported efficiently while minimizing energy use and wear on the equipment.
6. Managing Slurry Concentration
The concentration of solids in the slurry plays a key role in the performance of slurry lines. High concentrations of solids can cause clogs and increase the wear on the pipeline. On the other hand, low concentrations of solids may result in inefficient transport.
It’s important to maintain the proper concentration for the type of slurry being transported. This can be achieved by adjusting the flow rate or adding additional liquid to the system as needed.
Troubleshooting Common Issues in Slurry Lines
Even with the best practices in place, they may still face challenges. Understanding common issues and how to address them can help maintain optimal performance.
Blockages and Clogging
Blockages are one of the most common issues in slurry lines. These occur when the slurry’s solid particles settle or accumulate, blocking the flow. Clogs can often be avoided by maintaining an optimal flow rate and regularly cleaning the system.
Wear and Tear
Wear and tear are inevitable, especially in slurry lines that transport abrasive materials. Using lined slurry pumps and pipes can significantly reduce wear and prolong the life of the system. However, periodic inspections are still necessary to catch early signs of damage.
Inefficient Material Transport
If a slurry line is underperforming, it may be due to a variety of factors, including incorrect pipe material, inadequate pump capacity, or improper flow conditions. Regular monitoring and maintenance are essential to identify and rectify any inefficiencies.
The Role of Technology in Slurry Line Optimization
Advancements in technology have greatly improved the ability to optimize slurry lines. Automation, real-time monitoring, and data analytics all contribute to better performance and reduced downtime.
Automation and Control Systems
Automated control systems can adjust the flow rate, pressure, and other parameters in real-time, ensuring optimal conditions for slurry transport. Automation helps reduce human error and ensures that the system operates efficiently.
Real-Time Monitoring
Using sensors and flow meters, operators can continuously monitor the performance of slurry lines. These systems provide real-time data on key parameters like pressure, temperature, and velocity, allowing for immediate corrective action if needed.
Data Analytics for Predictive Maintenance
Data analytics tools can be used to predict when components of the slurry line may need maintenance or replacement. By analyzing historical data, these tools can identify patterns that indicate potential issues, allowing for proactive maintenance and minimizing downtime.
Conclusion
Optimizing them is crucial for enhancing the efficiency and reliability of material transport systems. Selecting the appropriate materials for the pipeline, such as lined slurry pipes or composite materials, is key to ensuring durability and minimizing wear. It’s also essential to maintain optimal flow conditions, adjusting factors like velocity and pressure to prevent issues such as clogging or excessive erosion.
Regular maintenance practices, such as routine inspections and cleaning, help identify wear and tear early, preventing costly breakdowns. By replacing worn-out components and addressing issues promptly, industries can extend the lifespan of them and avoid unexpected downtime.
Incorporating technology like automation and real-time monitoring systems takes optimization to the next level. Automated systems can adjust flow rates, pressure, and other parameters in response to changing conditions, ensuring consistent performance. Real-time monitoring allows for continuous tracking of slurry conditions, helping detect problems early and enabling proactive management.
By implementing these best practices, industries can significantly reduce downtime, minimize maintenance costs, and improve the overall efficiency of their slurry transport systems. This results in more reliable operations, lower costs, and enhanced productivity across industries that rely on slurry lines for material transport.
Have Questions?
Get in touch with us now!
Related Blogs
Key Components of an HDPE Fusion Machine and Their Functions Explained
Introduction Understanding the HDPE Fusion Machine Key Components of an HDPE Fusion Machine How HDPE Fusion Works: From Setup to Solid Joint Performance and ROI
Advancements in Dredging Technology: Automation, GPS, and Real-Time Monitoring
Introduction What Is Modern Dredging Technology? Core Technological Advances Reshaping Dredging Application Benefits Across Key Industries Remote Operations and Cloud Connectivity Sustainability and Compliance Built
Key Engineering Considerations for Installing Irrigation Pipe Floats in Uneven Terrain
Introduction Purpose of Irrigation Pipe Floats Engineering Challenges in Uneven Terrain Design and Installation Considerations Addressing Common Mistakes in Irrigation System Installation Performance Benefits of